|

|
|
|
|
Nella formazione del vetro, elemento che non presenta un punto di fusione netto, si lavora in un range di temperatura in cui esso è allo stato plastico. I limiti di tale intervallo oscillano tra picchi massimi detti "punti di aggregazione", in cui la temperatura è di 1100 °C circa, e livelli minimi, detti "punti di trasformazione", in cui la temperatura è intorno a 800 °C.
|
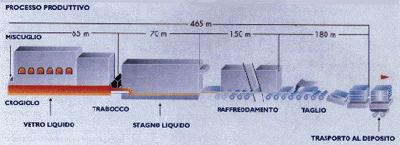
La fabbricazione e la lavorazione del vetro si articolano in quattro fasi: fusione, formatura, ricottura e finitura.
Fusione: è la fase iniziale, durante la quale, la carica, formata da componenti diversi tra loro, viene polverizzata e mescolata a rottami di vetro che agiscono da fondente. Durante la fusione, si verificano l'eliminazione dell'acqua presente nei componenti di partenza, la dissociazione dei carbonati e dei solfati con sviluppo di anidride carbonica o solforosa, la formazione di una massa fusa il più possibile omogenea.
Affinaggio o affinazione (2° momento della fusione): è l'operazione con cui la massa fusa viene privata di tutte le bollicine di gas presente, che potrebbero dare origine a difetti nei manufatti preparati. In questa fase, si assiste alla deposizione sul fondo del forno delle parti non fuse e all'arrivo in superficie delle bolle di gas formatesi durante la fusione. Tali bolle sono originate dalla decomposizione dei carbonati e dei solfati iniziali in ossidi e anidride carbonica o solforica.
L'affinazione viene realizzata aggiungendo alla massa fusa piccole percentuali di agenti affinati. Questi facilitano notevolmente l'operazione, in quanto fanno aumentare il volume delle bolle e ne provocano l'espulsione, oppure permettono la diminuzione della solubilità dei gas nel vetro. Conclusa questa fase, il vetro fuso è una massa avente in tutti i punti uguale composizione chimica e, conseguentemente, le medesime proprietà fisiche.
E' possibile, a questo punto, operare una decolorazione del vetro, tramite l'ossidazione di sali di ferro.
La fusione si conclude con la fase di riposo o di condizionamento, durante la quale la massa fusa viene raffreddata gradualmente fino alla temperatura di foggiatura o di formatura.
La fase seguente è la formatura, eseguita in diverse modalità, quando il vetro è ancora fluido e si trova in un campo di temperatura nel quale assume viscosità tale da poter essere lavorato e da conservare la forma impartita, senza alterazioni.
La ricottura consiste in un riscaldamento del vetro fino alla temperatura superiore di ricottura e serve ad eliminare le torsioni che si generano durante la formatura e che rendono difficile le operazioni di finitura come, ad esempio, il taglio. E' una fase essenziale per eliminare le tensioni interne formatesi per irregolarità di riscaldamento o raffreddamento.
La scelta della temperatura e della velocità di raffreddamento sono in funzione del tipo di vetro e del suo spessore. Dopo aver raggiunto la temperatura dovuta, l'oggetto viene mantenuto in tale stato per un periodo sufficiente ad assicurare il raggiungimento dell'uniformità termica in ogni suo punto; quindi viene raffreddato lentamente fino a una temperatura inferiore di 50 °C a quella di ricottura, ed infine viene portato rapidamente a temperatura ambiente.
Trattamenti speciali sono la siliconatura e la solforazione. La prima, utilizzata soprattutto per i contenitori, avviene nel forno di ricottura. La seconda necessita di una ricottura del vetro in ambiente SO2. Quest'ultimo determina la formazione di silicati alcalini solubili e quindi un depauperamento superficiale di alcali, con conseguente maggiore resistenza chimica.
Tipi di finitura
- Meccaniche: pulitura, molatura, smerigliatura, intaglio.
- Chimiche: opacificazione ottenuta tramite acido fluoridrico.
- Termiche: fusione locale per incollaggio di più parti, ricottura, tempra.
|
|
|
|
La tempra, è una fase in cui l'impasto vitreo, in seguito al riscaldamento fino a circa 700 °C, viene bruscamente raffreddato con getti di aria fredda, acquisendo un'alta resistenza meccanica superficiale. La tecnica determina la creazione di tensioni permanenti di compressione sulla superficie del vetro, bilanciate all'interno da equivalenti tensioni di trazione. La tempra è effettuata in impianti costituiti da un forno nel quale si ha una variazione di temperatura da +3 °C a -3 °C, così che la resistenza meccanica del vetro alla trazione, all'urto ed allo sbalzo termico, viene aumentata da 3 a 5 volte. |
La tempra chimica, utilizzando lo scambio ionico, consente la produzione di vetri con proprietà di resistenza alla flessione fino a 7000 kgp /cm2.
Ad esempio, un vetro con ossido di litio, immerso in cloruro sodico fuso, provoca: uno scambio ionico superficiale con sostituzione fra gli ioni di sodio e quelli di litio, la creazione di uno strato superficiale in compressione e un miglioramento del grado di resistenza meccanica del vetro. Altra variante consiste nel formare in superficie uno strato devetrificato a coefficiente di dilatazione inferiore al vetro, con un guadagno in compressione due o tre volte maggiore rispetto alla tempra termica.
Dal punto di vista termico, la lavorazione del vetro si articola nelle seguenti fasi:
- Innalzamento termico progressivo (grazie all'utilizzo gas metano come combustibile che permette di raggiungere alte temperatura) della durata di 6 ore fino ad arrivare alla fase della fusione.
- Fase di fusione: a 1500 °C. Durata di 6 ore
- 1° fase di affinaggio : a 1300 °C. Durata 6 ore
- 2° fase di affinaggio : a 1200 °C. Durata 6 ore
- Fase di formatura per colata: tra 1100 e 1000 °C. Durata inferiore all'ora
- Fase di formatura per soffiatura e pressatura: inferiore ai 1000 °C. Durata di un'ora circa.
|
|
|